What is Porosity in Welding: Best Practices for Staying Clear Of Porous Welds
What is Porosity in Welding: Best Practices for Staying Clear Of Porous Welds
Blog Article
Comprehending Porosity in Welding: Exploring Causes, Effects, and Prevention Methods
Porosity in welding is a consistent difficulty that can considerably influence the high quality and stability of welds. As specialists in the welding market are cognizant, comprehending the reasons, impacts, and avoidance strategies connected to porosity is crucial for achieving durable and trustworthy welds. By delving into the origin of porosity, examining its detrimental impacts on weld quality, and exploring effective prevention strategies, welders can improve their expertise and abilities to create top quality welds consistently. The intricate interaction of factors adding to porosity needs a comprehensive understanding and an aggressive method to guarantee effective welding end results.
Typical Root Causes Of Porosity
Porosity in welding is mainly brought on by a mix of aspects such as contamination, improper securing, and poor gas protection throughout the welding procedure. Contamination, in the kind of dust, oil, or corrosion on the welding surface area, creates gas pockets when warmed, resulting in porosity in the weld. Incorrect protecting occurs when the shielding gas, frequently utilized in procedures like MIG and TIG welding, is unable to totally protect the molten weld pool from reacting with the bordering air, causing gas entrapment and subsequent porosity. Additionally, inadequate gas coverage, often as a result of wrong circulation rates or nozzle positioning, can leave components of the weld vulnerable, permitting porosity to develop. These elements collectively add to the formation of voids within the weld, weakening its integrity and potentially causing architectural issues. Recognizing and resolving these usual reasons are important actions in preventing porosity and making certain the quality and toughness of bonded joints.
Effects on Weld Quality
The visibility of porosity in a weld can considerably jeopardize the overall quality and integrity of the welded joint. Porosity within a weld develops gaps or dental caries that deteriorate the framework, making it more susceptible to breaking, deterioration, and mechanical failing. These gaps act as stress and anxiety concentrators, decreasing the load-bearing ability of the weld and raising the chance of early failing under applied stress. On top of that, porosity can additionally offer as possible sites for hydrogen entrapment, additional exacerbating the degradation of the weld's mechanical properties.
Furthermore, porosity can impede the effectiveness of non-destructive testing (NDT) methods, making it testing to detect various other defects or suspensions within the weld. This can cause substantial safety issues, especially in critical applications where the structural integrity of the welded elements is paramount.
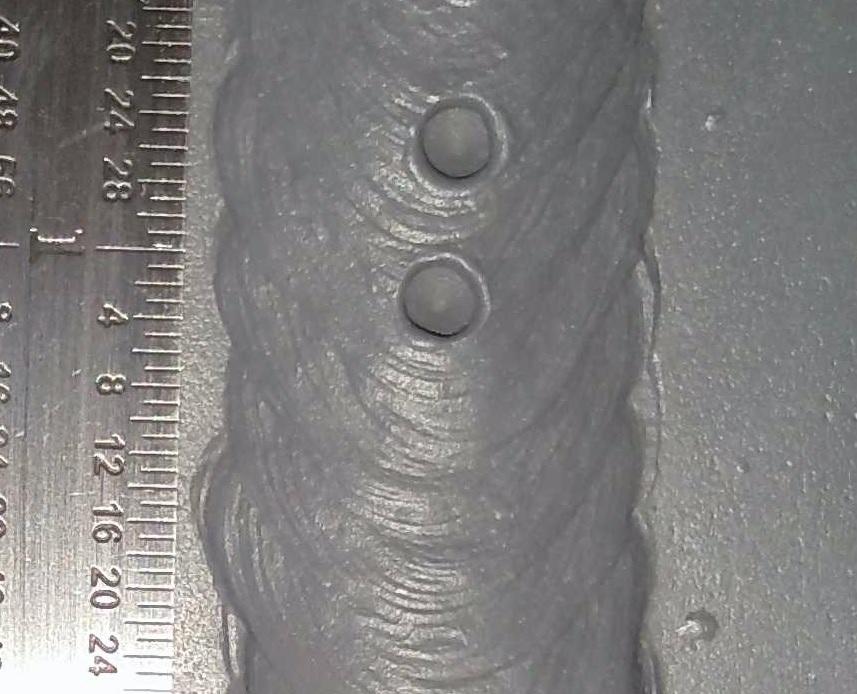
Avoidance Techniques Introduction
Given the detrimental effect of porosity on weld high quality, effective prevention techniques are critical to keeping the architectural honesty of welded joints. Furthermore, choosing the ideal welding specifications, such as voltage, existing, and travel rate, can assist reduce the threat of porosity development. By incorporating these prevention methods into welding techniques, the incident of porosity can be dramatically minimized, leading to stronger and more dependable bonded joints.
Significance of Proper Protecting
Proper protecting in welding plays a critical duty in avoiding atmospheric contamination and making certain the stability of welded joints. Protecting gases, such as argon, helium, or a mixture of both, are typically utilized to shield the weld pool from reacting with components airborne like oxygen and nitrogen. When these reactive aspects enter contact with the warm weld swimming pool, they can trigger porosity, resulting in weak welds with lowered mechanical buildings.
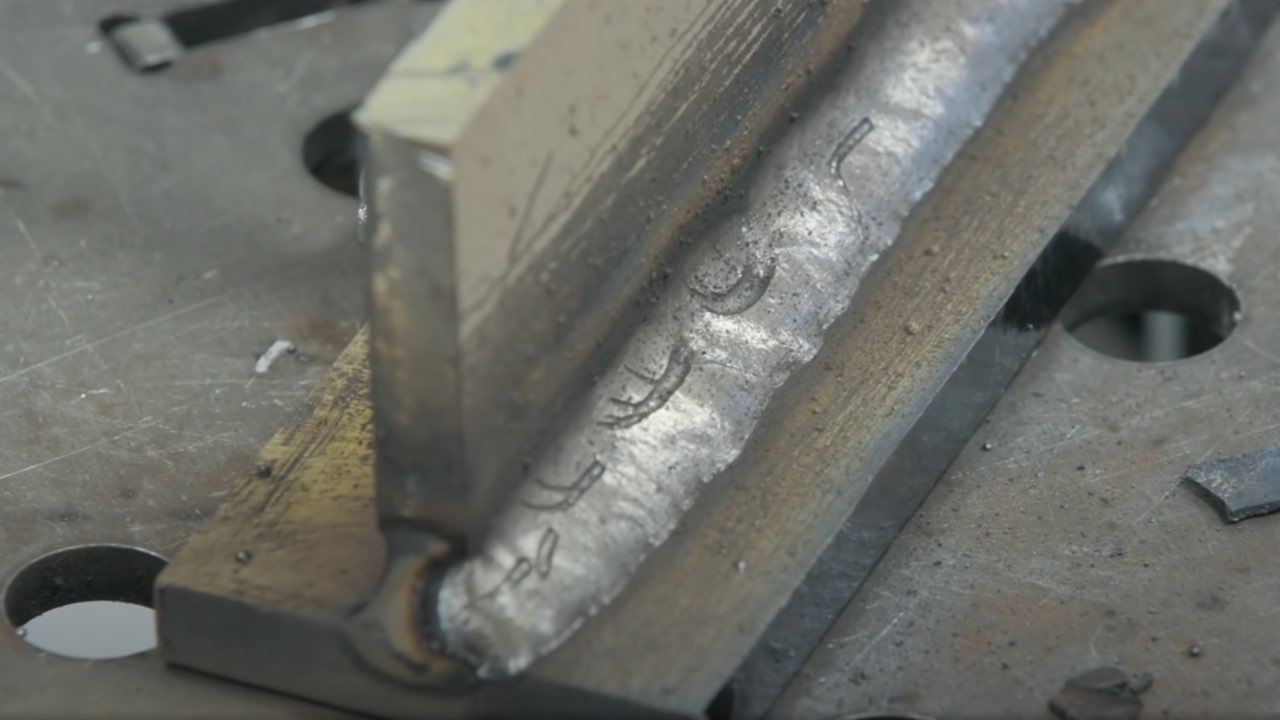
Inadequate shielding can cause various defects like porosity, spatter, and oxidation, jeopardizing the architectural honesty of the bonded joint. As a result, sticking to proper shielding methods is important to generate top notch welds with marginal flaws and make certain the longevity and reliability of the bonded parts (What is Porosity).
Tracking and Control Techniques
Just how can welders effectively keep an eye on and regulate the welding process to make sure optimal outcomes and stop defects like porosity? One trick approach is with using advanced monitoring technologies. These can consist of real-time surveillance systems that offer responses on criteria such as voltage, present, take a trip rate, and gas circulation rates. By continually checking these variables, welders can recognize variances from the optimal conditions and make instant adjustments to stop porosity development.

Furthermore, executing proper training programs for welders is important for checking and controlling the welding procedure properly. What is Porosity. Informing welders on the significance of keeping constant specifications, such as appropriate gas securing and travel rate, can assist visit the website stop porosity concerns. Routine assessments and accreditations can likewise guarantee that welders are skillful in surveillance and regulating welding procedures
Additionally, making use of automated welding systems can improve tracking and control capabilities. These systems can exactly regulate welding parameters, lowering the chance of human mistake and making sure constant weld top quality. By combining sophisticated tracking technologies, training programs, and automated systems, welders can efficiently keep an eye on and control the welding procedure to lessen porosity defects and attain high-grade welds.
Verdict

Report this page